Thermocouples were invented in 1821 by Thomas Johann Seebeck, an important German physicist. Seebeck was trying to understand how different materials conduct heat when he noticed that an electric current could be generated when two different metals were brought into thermal contact.
Later, Seebeck discovered that this current depended on the temperature difference between the two metals. This fundamental discovery led to the creation of the thermocouple, a device that converts temperature difference into an electric current. The first thermocouples were made of two wires of different metals, such as copper and iron, welded together at the ends.
Thermocouples have become important temperature measurement tools due to their ability to detect even small temperature variations and function in extreme conditions such as high pressures, corrosive environments, electromagnetic vibrations, etc.
Today, thermocouples are used in a wide range of applications, from aerospace industry to electricity production, steel production, glass production, and many other industrial and scientific applications.
Operating principles of thermocouples
In thermocouples, the junction that is exposed to the temperature being measured is called the hot junction or measurement junction. In contrast, the junction between the thermocouple conductors and the measuring circuit is called the cold junction or reference junction.
To measure temperature with a thermocouple, it is necessary for the reference junction to be at a known temperature, usually 0°C, so that the generated electromotive force (EMF) depends solely on the temperature of the measurement junction.
Measurement methods with thermocouples can generally be divided into two types. The first involves directly connecting the thermocouple to a voltmeter, or through compensation or extension wires. The second method involves keeping the cold or reference junction at a constant and known temperature, usually 0°C, so that the generated EMF depends solely on the temperature of the measurement junction.
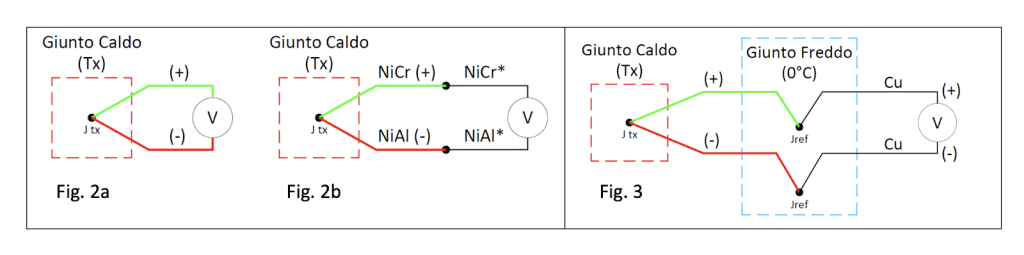
Apart from the different sizes of the wires, which affect the higher or lower resistance and durability of the thermocouple, the type of insulation and protection of the thermocouple is of considerable importance. The applicability of the thermocouple in chemically non-inert environments, especially at high temperatures, depends on these characteristics.
In these cases, the thermocouple is generally coated with a flexible sheath or a ceramic material that is resistant to high temperatures. This coating serves both to ensure adequate electrical insulation of the wires from each other and from the surrounding environment, and to protect the thermocouple elements from chemical attack.
In selecting the materials for thermocouple construction, there are various requirements to be met, such as the temperature range used, cost, and application area.
Since 1996, CAP IT has designed and produced thermocouple temperature sensors and industrial heating blankets. CAP IT’s activity is characterized by advanced production, dynamic leadership, constant quality research, as well as experience, passion, enthusiasm, and a strong entrepreneurial spirit.
If you are looking for the ideal thermocouples for your activity, visit the CAP IT website!